Japanese Cone Kiln
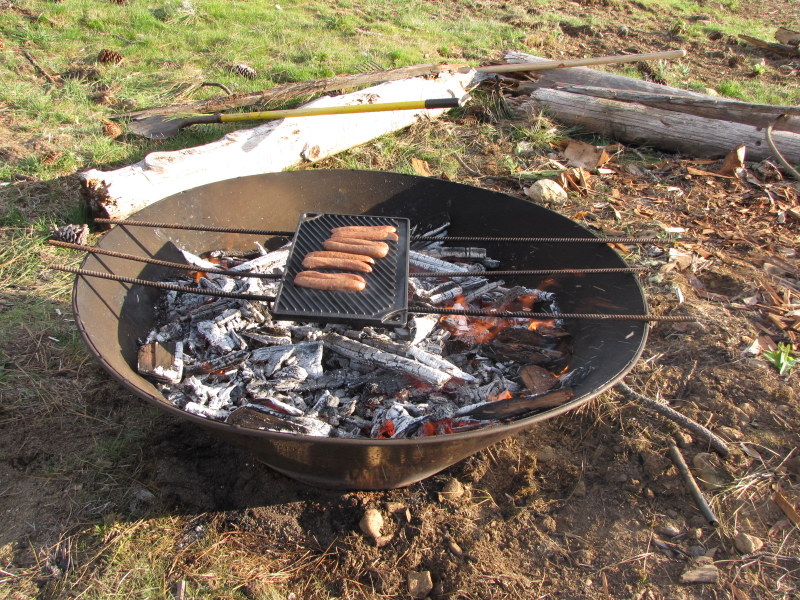
Kelpie Wilson has been playing with the Japanese Cone Kiln for Biochar see the latest on her site: http://www.greenyourhead.com/
She's finding that the Cone Kiln is easier to use than the alternatives and it produces more char too.
in her words:
I love my Japanese Cone Kiln. ... It is basically just a cone-shaped fire ring - a truncated cone. All you do is start a small fire in the bottom, and once that is all burned to glowing coals, you add small stick wood or branches on in layers. Each time the wood gets black and starts to ash, you add another layer. The layers underneath continue to cook out tar and gas, but they don't burn because air is excluded. When the cone is full you quench it with water. If you like, you can throw a grill on it and cook your dinner before you put it out.
It takes about 2 hours of very easy work. You can do other chores (like splitting wood) while you watch the fire. And the yield is very impressive. I start with two 6 cu ft wheelbarrows full of 2" kindling wood. I end up with about 5 cu ft of nice, crumbly biochar (water quenching really helps make your biochar hydrophilic).
Compare this with my JRO (Jolly Roger Oven) TLUD and my retort kiln, both using 55 gallon drums:
My JRO TLUD takes about 45 minutes when loaded with big wood chips. The yield is about 2 cu ft. Finding, screening and drying wood chips is a pain. And the tall stack of afterburner and chimney is hard to handle for me (at 5' 2" I need a step ladder).
My retort kiln takes about 2 hours to complete. The yield is about 1.5 cu ft and I usually use about one full wheelbarrow load of wood to fire it, sometimes more. The feedstock prep is similar to the cone kiln, although I can use any size wood to fire it.
Specifications of her cone kiln:
Here are quick specs on the cone kiln if you want to try making your own: It was made from a 4x8 sheet of 14 gauge steel with 3/8" rod welded around top and bottom rims for stability. Top diameter is 43". Bottom diameter is 16" and height is 16". It is open on the bottom so you just roll it away when you are done. That's it. My welder had a heck of a time bending the steel to make the seam weld. Needs a couple of strong guys or preferentially a differential slip roller to roll the form into shape. You could also make it from lighter weight steel.
or buy one: http://global.rakuten.com/en/store/tokiowalker/item/10005520-00/